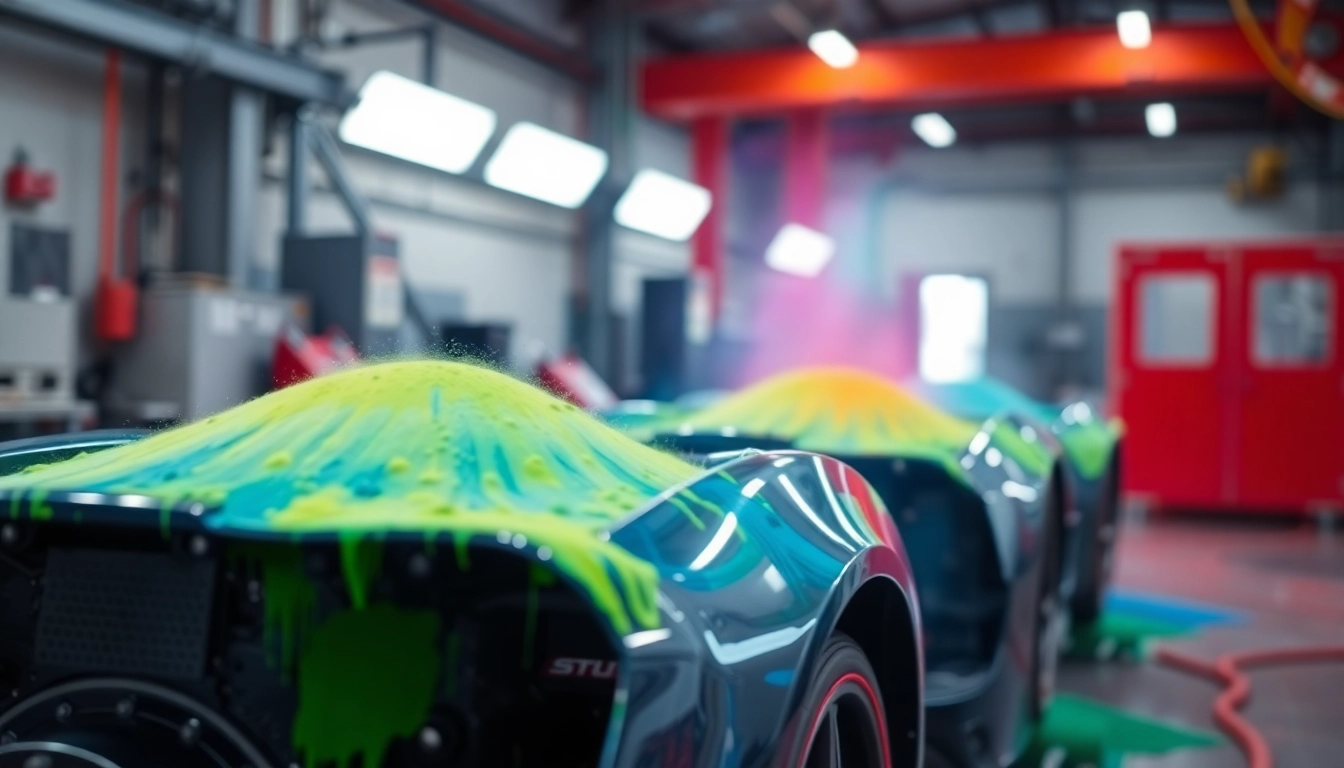
Understanding Powder Coating Basics
Powder coating is a widely-used finishing process that offers a durable and aesthetically appealing alternative to liquid paints. Unlike traditional coatings that use solvents, powder coating is applied as a dry powder, which is then cured under heat to form a robust finish. This unique process provides not only a highly resistive surface to corrosion and wear but also allows for a variety of colors and finishes. As industries continue to prioritize sustainability and efficiency, the popularity of powder coating has skyrocketed, becoming an essential choice for manufacturers, businesses, and DIY enthusiasts alike.
What is Powder Coating?
Powder coating refers to a process where a powdered form of paint is electrically charged and sprayed onto a surface. The powder consists of finely ground particles of pigment and resin, and once applied, it adheres electrostatically to the surface. After application, the coated item is cured in an oven to allow the powder to melt and form a durable, even coating. This process is likened to a “baking” of the material, resulting in a tough finish that is resistant to scratching, chipping, fading, and wearing compared to conventional paint.
Advantages of Choosing Powder Coating
Choosing powder coating over traditional liquid paint brings several advantages:
- Durability: Powder coating provides a thicker, tougher finish that is more resistant to chipping, scratching, and wear.
- Environmentally Friendly: It contains fewer volatile organic compounds (VOCs), making it a cleaner option that poses less harm to the environment.
- Color Variety: Powder coatings come in a wide array of colors and finishes, including metallic, matte, and textured options.
- Cost-Effective: Although initial application costs can be higher, the longevity and durability of powder coatings lead to lower maintenance and replacement costs over time.
- Easy Application: The powder coating application process can be streamlined through modern equipment, allowing for faster project turnaround.
Common Applications of Powder Coating
Powder coating is highly versatile and is utilized across various industries:
- Automotive: Improves the aesthetics and durability of vehicle parts such as wheels, frames, and bumpers.
- Furniture: Commonly applied on metal furniture for exterior and interior use, providing a weather-resistant and attractive finish.
- Construction: Used on metal building components, including railings, doors, and window frames.
- Consumer Goods: Frequently found on products like appliances, tools, and outdoor equipment for added durability and aesthetics.
- Architectural Elements: Enhances the lifespan and beauty of architectural features such as aluminum storefronts and metal structures.
The Powder Coating Process Explained
Preparation: Cleaning and Pre-Treatment
The first step in the powder coating process is surface preparation, which is crucial for achieving a high-quality finish. This includes cleaning the surface to remove any dirt, oil, rust, or existing coatings. Common cleaning methods include:
- Sanding: Manually or mechanically sanding surfaces to create a smooth base.
- Washing: Using detergents or solvents to remove contaminants.
- Pre-treatment: Applying a chemical solution or rinse that enhances adhesion and prevents corrosion.
Proper preparation ensures that the powder coating adheres well and provides maximum durability.
The Coating Application Process
Once the surface is prepared, the next step is the application of the powder coat. The process involves:
- Electrostatic Spraying: The powder is charged with electricity and sprayed onto the grounded metal surface, allowing it to attract and stick to the surface evenly.
- Fluidized Bed Coating: For thicker applications, parts can be preheated, and then dipped into a fluidized bed of powder. The heat causes the powder to melt and coat the surface.
After spraying, the coated object is inspected for uniformity and coverage before curing.
Curing: Baking for Durability
The final step in powder coating is curing. This involves placing the coated items in a curing oven where they are subjected to high temperatures, typically between 350°F to 400°F (about 177°C to 205°C). This stage allows the powder to melt, flow, and chemically react to form a solid, cohesive finish that is resistant to abrasion, corrosion, and impact.
After curing, the items are removed from the oven and are allowed to cool, resulting in a tough, durable surface.
Cost Considerations for Powder Coating
Average Costs for Different Projects
The cost of powder coating can vary widely based on several factors, including the size of the item, type of powder used, and preparation required. On average, powder coating costs range from $50 to $430 per item, with most consumers spending around $170.
Specific factors that can influence costs include:
- Item Size: Larger items typically require more powder and longer application times, increasing costs.
- Type of Powder: Specialty powders that offer unique colors or finishes may cost more.
- Complexity of Preparation: Items that require significant surface preparation or multiple coats will incur higher costs.
Factors Influencing Powder Coating Pricing
While planning your budget for powder coating, consider these additional influencing factors:
- Volume Discounts: Many powder coating companies offer discounts for larger orders, so it’s advisable to inquire about volume pricing.
- Location: Prices can vary by geographic area based on labor costs and market demand.
- Shipping Costs: If items need to be shipped to a coating facility, this can add to the overall cost.
DIY vs Professional Powder Coating: A Cost Comparison
DIY powder coating can save money, but it requires a significant upfront investment. Equipment such as a powder coating gun, curing oven, and various safety gear can cost several hundred dollars. Additionally, individuals must also account for the learning curve and the potential for mistakes that can compromise quality.
On the other hand, professional powder coating services provide assurance of expertise and equipment quality. They can often deliver better results in less time since they have trained personnel and more advanced machinery. Ultimately, the choice between DIY and professional services should align with your budget, project requirements, and desired quality level.
Choosing the Right Powder Coating Colors and Finishes
Popular Colors in the Industry
Packing a visual punch, the right color selection can significantly enhance the appeal and value of the coated item. Some popular colors frequently requested in the industry include:
- Black: A classic and versatile choice for most applications.
- White: Clear and clean, suitable for a modern look.
- Metallic Shades: Adds depth and glamour to parts, especially in automotive applications.
- Custom Colors: Many coating services now offer the ability to create custom shades, giving clients a unique edge.
Types of Finishes: Matte vs Glossy
The finish type also plays a significant role in design aesthetics:
- Matte Finishes: Provide a subtle and elegant look, often preferred for modern designs. They are also less prone to showing fingerprints or smudges.
- Glossy Finishes: Offer a shinier, reflective appearance, which can help accentuate colors. This finish tends to be easier to clean but may show imperfections more readily.
The choice between matte and glossy ultimately comes down to personal preference, intended use, and the specific requirements of the project.
Tips for Customizing Your Powder Coating
Achieving a unique powder coating finish requires careful consideration and often includes:
- Testing Samples: Before settling on colors and finishes, consider getting samples to test how they appear under different lighting conditions.
- Combining Finishes: Utilizing a combination of matte and glossy finishes can create striking contrasts and visual interest.
- Incorporating Effects: Techniques such as texturing or applying clear coats over colored powders can further personalize the outcome.
Maintaining and Repairing Powder Coated Surfaces
Best Practices for Care and Maintenance
While powder coatings are durable, they still require some maintenance to ensure longevity. Here are some best practices:
- Regular Cleaning: Use a soft cloth and mild detergent to clean surfaces. Avoid harsh chemicals and abrasive materials that can damage the coating.
- Avoiding Excessive Heat: Keep powder-coated items away from extreme heat sources that may degrade the coating over time.
- Protection Against Scratches: Pad corners and edges of items to prevent accidental scratches, especially in high-traffic areas.
How to Handle Damage and Touch-Ups
In the event of chipping or scratching, prompt repair can extend the lifetime of powder-coated surfaces:
- Touch-up Paints: Many manufacturers offer touch-up paints that match the powder coating, allowing for seamless repairs.
- Re-coating: For extensive damage, it may be best to strip the area down and apply powder coating again.
Always follow the manufacturer’s instructions for the specific powder used to avoid incompatibility issues.
Long-Term Durability and Performance
One of the most highlighted benefits of powder coating is its long-lasting performance. With proper maintenance, a powder-coated item can last anywhere from 10 to 20 years or more without the need for significant refinishing. The resilience of a powder coating ensures that it maintains its color and texture over time, even when exposed to environmental stressors. A well-maintained powder-coated surface will continue to provide both aesthetic charm and functional benefits for years to come.